Introduction
Diesel generators play a crucial role in providing backup power to various industrial applications, ensuring uninterrupted operations in the event of a power outage. To ensure the reliability and performance of a diesel generator, factory acceptance testing (FAT) is conducted to verify that the unit meets the specified requirements and standards before installation at the site. 300kw diesel generator will delve into the importance of diesel generators in industrial settings, the components and working principles of a diesel generator, the significance of factory acceptance testing, and the key steps involved in conducting FAT for a diesel generator.
Importance of Diesel Generators in Industrial Settings
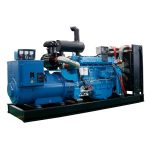
In industrial settings, uninterrupted power supply is essential to ensure the smooth operation of critical equipment and processes. Power outages can lead to significant downtime, resulting in production losses, financial implications, and potential safety hazards. Diesel generators serve as reliable backup power sources, providing electricity during emergencies or when the primary power source fails.
Diesel generators are widely used in various industrial applications, including manufacturing plants, data centers, hospitals, telecommunications facilities, and commercial buildings. These generators are preferred for their robustness, high efficiency, and ability to deliver power quickly in case of an emergency. With proper maintenance and regular testing, diesel generators can provide a reliable and cost-effective solution for ensuring continuous power supply in industrial environments.
Components and Working Principles of a Diesel Generator
A diesel generator consists of several key components that work together to convert diesel fuel into electrical power. The main components of a typical diesel generator include the engine, alternator, fuel system, cooling system, exhaust system, control panel, and base frame.
The engine is the primary component of the diesel generator and is responsible for converting the chemical energy stored in diesel fuel into mechanical energy. The engine drives the alternator, which is connected to the engine through a shaft. The alternator, also known as the generator, converts the mechanical energy into electrical power through the process of electromagnetic induction.
The fuel system of a diesel generator includes a fuel tank, fuel pump, fuel filters, and fuel injectors. The fuel pump draws diesel fuel from the tank and delivers it to the injectors, where it is atomized and injected into the combustion chamber of the engine. The fuel filters remove any impurities or contaminants from the fuel before it reaches the engine.
The cooling system of a diesel generator helps maintain the optimal operating temperature of the engine by dissipating excess heat generated during combustion. The cooling system typically consists of a radiator, cooling fan, water pump, and coolant reservoir. Proper cooling is essential to prevent overheating and ensure the efficient performance of the generator.
The exhaust system of a diesel generator is responsible for removing the combustion gases and emissions produced during the operation of the engine. The exhaust gases are directed through a series of pipes and mufflers to reduce noise levels and minimize environmental impact.
The control panel of a diesel generator houses the electrical components and controls that monitor and regulate the operation of the generator. The control panel includes features such as voltage regulators, frequency meters, circuit breakers, and monitoring instruments that provide real-time information about the performance and status of the generator.
The base frame of a diesel generator provides structural support and stability to the entire unit. The base frame is typically made of sturdy materials such as steel and is designed to withstand the vibrations and forces generated during the operation of the generator.
The working principle of a diesel generator involves the following steps:
1. The engine draws diesel fuel from the fuel tank and injects it into the combustion chamber.
2. The fuel is atomized and ignited by the compression of air in the combustion chamber, resulting in the generation of high-pressure gases.
3. The high-pressure gases push the piston downward, converting the chemical energy of the fuel into mechanical energy.
4. The mechanical energy drives the alternator, which converts it into electrical energy through the process of electromagnetic induction.
5. The electrical energy generated by the alternator is then delivered to the load or connected electrical system for use.
Significance of Factory Acceptance Testing (FAT)
Factory acceptance testing (FAT) is a critical step in the procurement and quality assurance process of a diesel generator. FAT is conducted at the manufacturer's facility before the generator is shipped to the installation site to ensure that it meets the specified requirements, standards, and performance criteria. FAT helps verify the functionality, reliability, and safety of the generator, while also providing an opportunity to identify and address any potential issues before installation.
The key objectives of factory acceptance testing for a diesel generator include:
1. Verification of Specifications: FAT ensures that the generator meets the technical specifications, design requirements, and performance criteria specified in the purchase order or contract. This includes confirming the rated power output, voltage levels, frequency, fuel consumption, emissions levels, and other relevant parameters.
2. Functional Testing: FAT involves testing the functional operation of the generator under various load conditions to verify that all components and systems are working correctly. This includes testing the engine, alternator, control panel, fuel system, cooling system, and other critical subsystems to ensure proper integration and functioning.
3. Performance Evaluation: FAT evaluates the performance of the generator in terms of efficiency, power output, voltage and frequency regulation, response time, and other key performance indicators. Performance testing helps validate that the generator can meet the power requirements of the intended application and perform reliably under normal and emergency conditions.
4. Safety and Environmental Compliance: FAT assesses the safety features, protection mechanisms, and environmental compliance of the generator to ensure that it meets industry standards and regulations. This includes verifying the presence of safety devices, emergency shutdown systems, exhaust emissions control, noise levels, and other safety and environmental requirements.
5. Documentation and Certification: FAT generates comprehensive documentation, test reports, and certification records that provide evidence of compliance with the specified standards and requirements. The documentation includes test procedures, test results, inspection reports, and any deviations or corrective actions taken during the testing process.
Key Steps in Conducting Factory Acceptance Testing for a Diesel Generator
The process of conducting factory acceptance testing for a diesel generator involves several key steps to ensure thorough and systematic evaluation of the unit. The following are the essential steps involved in FAT for a diesel generator:
1. Pre-Test Preparation: Before commencing the factory acceptance testing, the testing team should review the technical specifications, test procedures, and acceptance criteria outlined in the purchase order or contract. The test plan should be developed based on these requirements, including the specific tests to be conducted, test equipment to be used, and acceptance criteria to be met.
2. Visual Inspection: The first step in FAT is to conduct a visual inspection of the diesel generator to verify that all components are present, properly installed, and free from any visible defects or damage. The inspection should cover the engine, alternator, control panel, fuel system, cooling system, exhaust system, base frame, and other critical components.
3. Functional Testing: Functional testing involves verifying the operation of the generator under various load conditions to ensure that all systems and components are functioning as intended. This includes testing the starting sequence, load acceptance, voltage regulation, frequency control, fuel supply, cooling performance, and other key functions of the generator.
4. Performance Testing: Performance testing evaluates the power output, efficiency, response time, and other performance characteristics of the generator under different operating conditions. Performance tests should be conducted at various load levels to validate that the generator can meet the specified power requirements and performance criteria.
5. Safety and Environmental Testing: Safety and environmental testing assesses the compliance of the generator with safety standards, protection mechanisms, and environmental regulations. This includes testing the emergency shutdown systems, overcurrent protection, grounding systems, exhaust emissions, noise levels, and other safety and environmental features of the generator.
6. Load Bank Testing: Load bank testing is performed to simulate real-world operating conditions and evaluate the generator's performance under full load conditions. The generator is connected to a load bank that draws the specified load from the generator, allowing for testing of the power output, voltage regulation, frequency stability, and overall performance under maximum load.
7. Documentation and Reporting: Throughout the factory acceptance testing process, comprehensive documentation should be maintained, including test plans, test results, inspection reports, photographs, and any deviations or corrective actions taken. A final acceptance report should be prepared summarizing the test findings, compliance status, and any recommendations for further actions or improvements.
8. Customer Inspection and Approval: Once the factory acceptance testing is completed, the customer or their authorized representative should conduct a final inspection of the generator to verify that all requirements have been met. The customer's approval is required before the generator can be shipped to the installation site for commissioning and operation.
Conclusion
Factory acceptance testing is a crucial step in the procurement and quality assurance process of a diesel generator, ensuring that the unit meets the specified requirements and standards before installation in an industrial setting. By conducting thorough and systematic FAT, manufacturers, suppliers, and end-users can verify the functionality, reliability, and performance of the generator, while also ensuring compliance with safety and environmental regulations. FAT helps minimize the risks of equipment failure, downtime, and safety hazards, while also providing confidence in the reliability and performance of the generator in critical applications. By following the key steps outlined in this article, stakeholders can effectively conduct factory acceptance testing for a diesel generator and ensure the seamless integration and operation of the unit in industrial settings.